Downloads
Software, Technical Documentation, Drivers, Tutorials. Click here to find the information you need to have the best experience with Altus products.
Technical Support
On-call service 0800 510 9500
support@altus.com.br
Skype: Altus Support
Unavailable on Sundays and holidays
Knowledge Base
Click here to access tutorials, instructions and application examples created by our specialists to qualify your experience with Altus products and solutions!
Industries we serve
Solutions
Companys which trust Altus
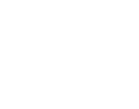
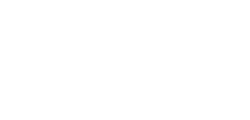
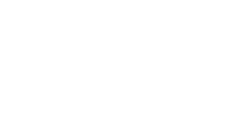
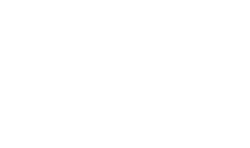
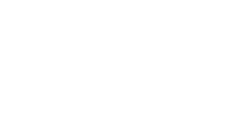
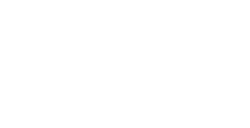
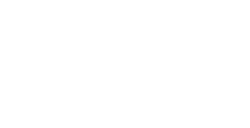
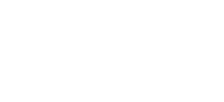
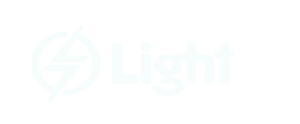
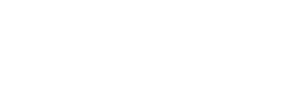
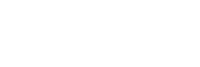
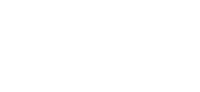
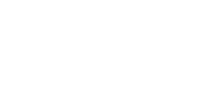
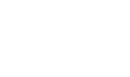
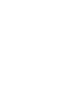
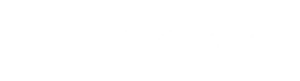
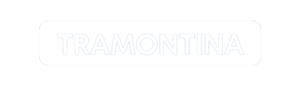
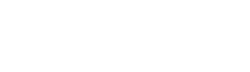
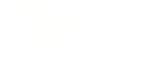
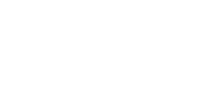
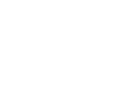
What our customers say about us
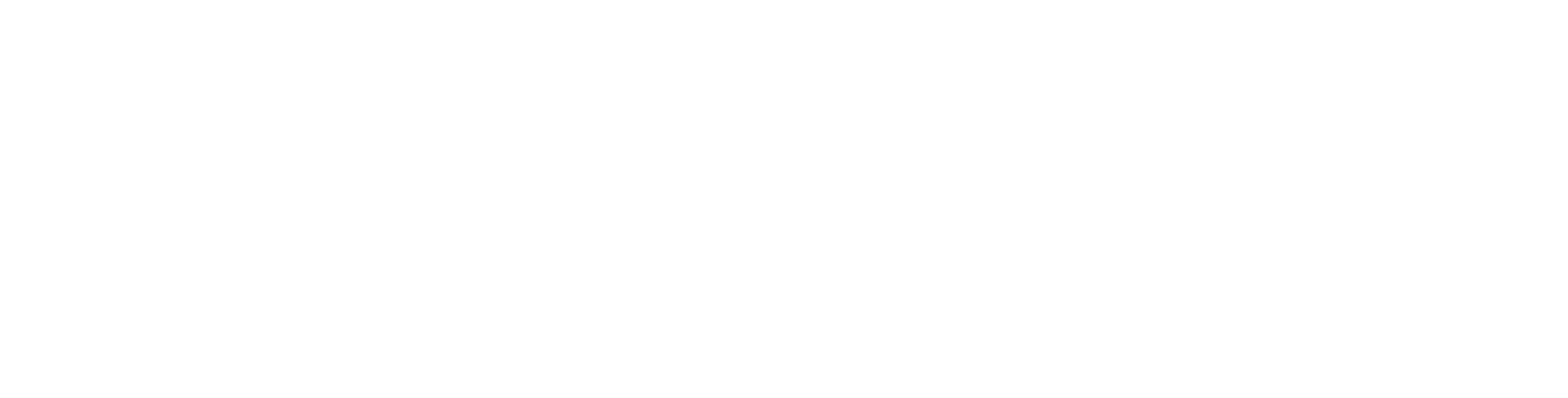
“Optamos por utilizar os produtos da Altus neste projeto por ser uma empresa consolidada, com 40 anos no mercado, e, também, devido à nossa política de priorizar a indústria nacional” – Carmelo Leão
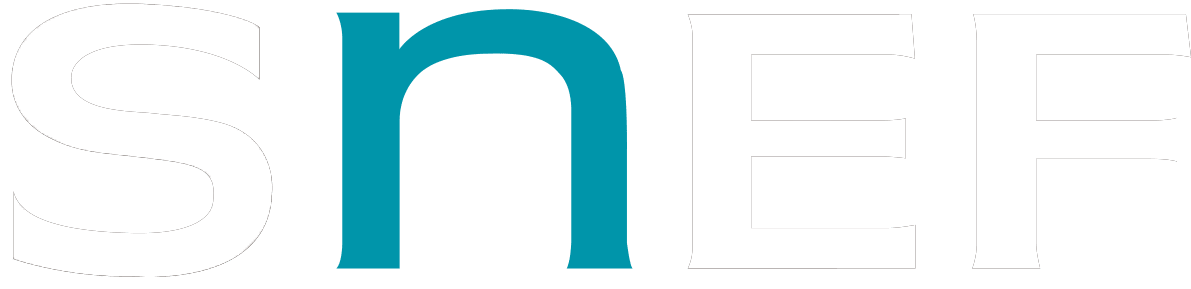
“A SNEF é cliente da Altus há alguns anos, então possuíamos experiência com os equipamentos desde a Série Hadron Xtrom até a Nexto Xpress. Por isso, tínhamos certeza da capacidade da Altus, tanto em relação aos representantes que nos atendem quanto com o suporte técnico” – Felipe Moreira
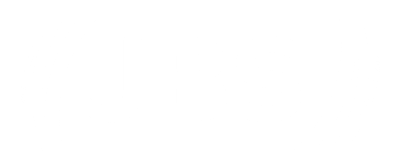
“Essa independência que eu tenho com os CLPs da Altus é gratificante demais. Dá muita segurança no dia a dia. Eu acredito e confio no produto de vocês (Altus)” – Jairo Quadros
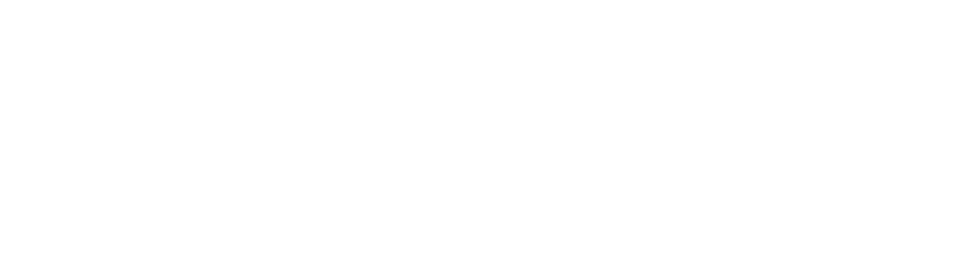
“A empresa possui um suporte que não vemos em outros lugares. O fato de poder contar com o suporte da Altus é fundamental para gente” – Paulo Aranha